Pressure and flow value optimization are an integral part of irrigation system design. With constant and often dramatic fluctuations in demand flow and supply pressure, valves and other components need to ensure dynamic pressure and flow control across the entire system.
<<Missed the webinar? Watch Now>>
In BERMAD’s webinar, “Pressure Reduction and Cavitation Prevention in Irrigation Systems” our Global Irrigation Unit Manager, Yiftah Enav, presented BERMAD pressure reduction and cavitation prevention principles, methods, systems and solutions. Yiftah shared useful insights about selecting the most effective pressure reducing control valves (PRVs) for long-term performance and cost savings.
During the webinar, questions regarding the theory of cavitation, erosion, velocity, ΔP and the practice of effectively screening, combining and allocating pressure reducing control valves were addressed:
Q: What is the difference between pressure reducing valves and proportional pressure reducing valves?
A: Pressure Reducing Valves (PRVs) are adjustable and are set to continuously reduce higher upstream pressure to a lower constant downstream pressure, regardless of changes in upstream pressure and/or demand flow.
Proportional Pressure Reducing Valves (PPRVs) do not include a pilot and are therefore not adjustable. Based on the ratio between the effective areas of their diaphragm and closure, PPRVs continuously reduce higher upstream pressure to lower downstream pressure in a constant ratio.
Only double chamber valves can serve as PPRVs.
Q: For all sizes, is the PD reduction factor 2.5?
A: The PD reduction factor is 2.5 in most of the series and sizes; however, the reduction factor can vary and can be found on our website, price lists and relevant product pages. Refer to the relevant reduction ratio table per each valve size and each valve series (100, 700).
Q: Can we use pressure reducing valves to reduce static pressure? Can a PRV work in no flow conditions?
A: Yes. When demand flow drops to zero, momentarily the flow reaching the line through the PRV is greater than the flow out of the line (which is zero). As a result – pressure accumulates and slightly rises in the line downstream from the PRV. The PRV pilot senses pressure above setting and closes the PRV, "trying" to reduce pressure back to setting. As the flow is zero (dead end), even when the valve is drip-tight shut, pressure will remain slightly above setting (assuming no leaks) ensuring the PRV remains shut.
Q: It has been claimed that it’s not always possible for the PRV to maintain P2 pressure when flow stops suddenly compared to a direct acting PRV. For this purpose, a pressure relief valve is required downstream of the PRV. What is your response to this claim?
A: Direct acting PRVs may be quicker than hydraulic PRVs, but are clearly inferior in terms of head loss, added features (even close/open), sensitivity, accuracy, maintenance and still require a pressure relief valve to protect the system should the DPRVs jam or fail to seal.
To quicken response time, a downstream pressure gourd pilot can be added or, referably, use a double chamber PRV.
Q: We set PRV at P1 to maintain required P2. In this condition, P1 is as per design (theoretically) but actually P1 changes due to partly operation of area, variation in demand, pump operation or leakage. What is P2 pressure during this condition? Does it change (increase)? Do we need to go to site again to set pressure or does it automatically maintain P2 pressure? Also, what will happen to the flow during variation as P1 changes?
A: Pressure reducing valves are controlled continuously by a pressure reducing pilot that only senses P2. Changes in demand and/or P1 that affect P2 are immediately sensed by the pilot and cause its internal devices to change position and instantly throttle the valve close (@ P2 Rise) or open (@ P2 drop) to reach pilot setting.
The flow is determined by the system emitters and outlets, not by the PRV. In fact, the PRV automatically adjusts its opening rate to the actual demand (& P1) obtaining it’s not “too open” or “too closed” to always maintain the set P2.
Q: What are the practical differences between PRV’s with two-way and three-way controls? Since a three-way loop is vented to atmosphere, will it impact on the regulation stability of a diaphragm actuated valve?
A: A three-way circuit is characterized by the pilot “selecting” the water route: P1 to control (closing) or control to vent (opening). This leads to using a very small volume of control water and results in two different behaviors:
- Hysteresis (as a certain change needs to “accumulate” before passages in pilot “switch”) which considered as less sensitive but in high quality pilots is small enough. Hysteresis itself is sometimes essential to eliminate line pressure hunting by “breaking” the reaction chain in the system.
- Fully open at pressure drop (as pilot is venting, “canceling” all closing forces), which allows for energy savings. The vent to atmosphere sometimes leads to excessively fast opening, resulting in instability. This can easily be solved by applying a dripper or other restriction on the vent tube end.
<<Missed the webinar? Watch Now>>
Q: What is the +/- pressure loss through a two-way control loop?
A: A two-way circuit is characterized by continuous flow from P1 through a restriction into the control chamber while the pilot “connects” the control chamber to valve downstream, releasing chamber pressure as long as the valve is open. This leads to relatively high volume of control water (0.2-0.5m³/h; 0.9-2.2gpm) and results in sensitivity to dirty water with the below hydraulic behaviors:
- Near zero hysteresis as the pilot required travel to increase (opening) or decrease (closing) release flow is insignificant and therefore immediate. While this is a benefit, it is sometimes too sensitive and leads to hunting.
- Additional head loss (3-5m; 4.4-7psi) created due to the spring force + P2 in the control chamber. This added head loss disappears when the valve flow velocity exceeds ~2m/s; 6.6f/s and valve opening force (due to ΔP) exceeds the main valve’s spring force.
Q: What are the sizing criteria for circuit inlet restriction in two-way control?
A: Two-way control restriction should be smaller than the pilot water path to allow stable & accurate regulation together with smallest possible added head loss and sufficient reaction time. We can say the criteria is the size of the water path in the pilot which is linked with the valve size.
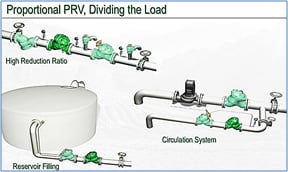
Q: What kind of applications can proportional pressure reducing valves be used for?
A: Gravitation downhill lines and/or when required ΔP is high and calls for two-stage pressure reduction to protect valves from erosion and cavitation and to provide backup protection to the system.
Q: While supplying downhill from a balancing reservoir to multiple minor irrigation tanks (i.e. direct discharge to the atmosphere as explained in the case of pressure breaking tanks), which types of PRVs can be used? Can you please shed some light on this?
A: The recommended solution to replace pressure breaking tanks (PBTs) is to apply PPRVs which has the following benefits:
- No level control valves
- Cost efficient infrastructure
- No “0” pressure downstream
- Immediate response – double chamber
- Maintenance free – no pilots, restrictions or filters
- No contamination
However, as the PPRV reduction ratio is constant, when the upstream pressure drops due to friction head loss in the line, so does the downstream pressure. As irrigation demand flow varies, we need to locate the PPRVs based on the elevation differences (maximum upstream pressure) and on the actual head at maximum flow/friction loss (minimum upstream pressure). Since each PPRV determines the pressure to the following PPRV – the design calculation is a bit challenging. BERMAD developed an Excel file to consider all parameters as a design support tool.
Q: What restrictions should be used for PPRVs?
A: PPRVs do not require any restrictions.
Q: Can a pressure reducing valve be designed based on flow as variable rather than outlet pressure as variable? Can we use a flow limit/control valve as an option for pressure reducing valve in some cases, such as a gravity line?
A: A number of issues need to be considered with respect to pressure and flow in pressure reducing valves:
- Pressure reducing valves only sense downstream pressure (P2). The flow is determined by the system water consumption downstream from the PRV (emitters, reservoirs, villages, etc.) Should demand flow rise and P2 drop, the PRV will “try” to increase P2 back to setting by opening (allowing more flow). If demand flow drops and P2 rises, the PRV will throttle close to reduce P2 back to setting (allowing less flow).
- One can either convert the PRV to a Flow Control Valve (FCV) or add a flow control feature to a PRV making it a pressure reducing & flow control valve.
- FCV is very much like PRV but instead of sensing the P2, the FCV pilot senses ΔP or ΔF (which is the hydraulic “expression” of flow) across an orifice plate, a pitot tube or a paddle located inside the flow. Should demand rise above setting (even when pressure is low), rising flow velocity will increase ΔP or ΔF and the FCV will throttle close to limit flow back to setting.
- Adding a flow control feature to a PRV making it a pressure reducing & flow control valve means we have two different pilots on the same valve. One controls the flow based on sensing ΔP or ΔF across
- an orifice plate, a Pitot tube or paddle; the other senses P2 and controls the valve accordingly.
Should demand rise and P2 drop, the flow pilot will take control to limit the flow back to setting. Should demand drop, the flow pilot allows the valve to open. Should P2 rise, due to P1 increase or demand drop, the reducing pilot will take control and throttle the valve close.
<<Missed the webinar? Watch Now>>
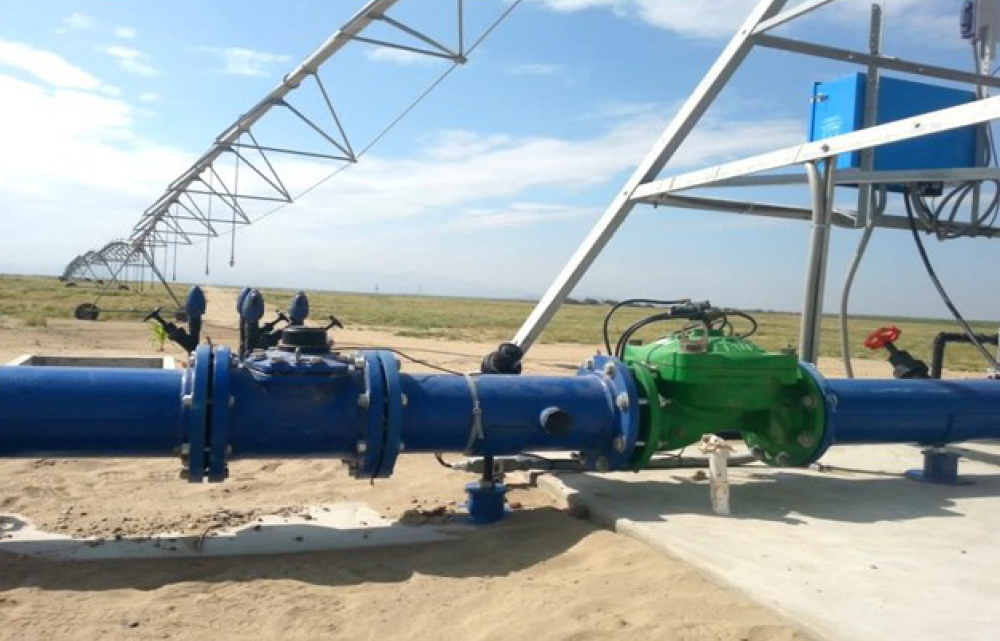
When the flow pilot is in control, the valve closes, resulting in P2 drop sometimes below setting of the reducing pilot, which is not dominating the valve and cannot raise P2 as long as demand is above the flow pilot setting. For that reason, it is recommended to set the flow pilot 15-20% above the nominal flow of the line.
Q: We installed four valves at the chak (main block) inlet where inlet pressure (P1) is 60m and 4 sub-chak (plot) valves have different pressure (P2) requirements (means P2 for Valve 1= 35m, Valve 2= 25m, Valve 3= 45m, Valve 4= 50m). The sub-chak’s distribution pipe length, diameter & elevation vary, but the same flow at the last end of each sub-chak outlet is required. So, can we maintain the same flow at the last end of the sub-chak outlet when P1 is constant, but P2 varies?
A: The answer depends on whether irrigation is pressurized & performed by drip/sprinklers/jets (any emitter with known flow) or we are dealing with flood irrigation where the distribution pipe end is open to the atmosphere.
- In pressurized MIS irrigation, the flow is determined by the accumulating flow of all the sub-chak’s emitters and is maintained as long as P2 is per design and no burst has occurred.
- In flood irrigation, pressure reducing is irrelevant as the line end is open. The right solution is a flow control valve which will leave low pressure in the distribution line (friction loss @ given flow + elevation).
<<Missed the webinar? Watch Now>>
Q: Can we remotely change the PRV setting for pressure and flow?
A: Pressure reducing valves (and all hydraulic control valves) can accept two pilots set to different pressures. Installing a solenoid to “select” between the pilots will allow remote switching between pressure regimes.
Other options require adding devices on the pilot to enable dynamic remote setting. This will also require special controllers to enable analog control.
Q: What is the optimum range for valve travel in hydraulic pressure reducing valves?
A: Somewhere between 15%-30% depending on valve type, pressure & flow conditions, annual operating time and other factors. Applying a V-port plug forces the PRV to open more to better handle low flows. This allows the PRV to be ~15% open even when flow velocity drops to ~0.5m/s.
Q: In a direct pumping distribution network, how the PRV will respond when a power failure occurs and upstream pressure rises suddenly? Will it able to maintain P2 downstream?
A: This is complex, as power failures are a multi-scenario event. Assuming the question refers to a PRV on one of the outlets from a main line connecting pump to a reservoir, we can expect the PRV to open when pressure drops due to a negative wave. In this case, it will probably not close fast enough to maintain P2 should a positive wave hit.
Q: Can the 400 series (single chamber, globe pattern) valve be used for pressure reducing applications? If yes, will it be more prone to cavitation compared to Y pattern valves (100 and 700 series)?
A: The 400 series can be used for pressure reducing applications. In fact, most of the metal PRV applications in irrigation are carried out by IR-400 Series or other single chamber valves. The IR-400 Series does not include a raised seat which makes them less resistant to cavitation damage than the IR-100 Series, due to it being made from composite material and the IR-700 Series which incorporates a raised stainless-steel seat. The Y Pattern also contributes to better cavitation resistance and ~25% better flow performance compared to standard globes.