What are Flow Control Valves?
Flow control valves are designed to maintain a constant pre-set maximum flow regardless of fluctuating demand or varying system pressure. Flow limiting is required at the outlets from main systems to consumers like secondary systems (main line to hydrant line; hydrant line to distribution line), reservoirs, etc. in order to protect the supplying system from over consumption. Consumption is determined by user demand downstream from the flow control valve — according to the number of emitters in the field and their flow data, number of users irrigating at the same time, exterior components like reservoirs and backup systems.
System flow versus time with flow limiting valve and without (dashed line)
Unable to control users, designers are using flow control valves to ensure that the flow won't exceed significantly above design flow. By limiting the flow, we protect the supply system from excess demand, prioritizing it over users when they attempt to consume more than the system’s specifications.
<< Download the free case study on Integrated Irrigation Management >>
Introduction
Irrigation modernization is aimed at saving water and energy by improving irrigation infrastructure — upgrading from flood irrigation to pressurized systems and by doing so, increasing irrigation efficiency & optimizing the usage of existing water resources. Hydraulic design of pressurized irrigation systems is based on two main parameters: flow rate & pressure. Based on these parameters, the entire system design is established: pumps are selected, the type & size of the filtration system are determined, main & distribution lines materials & diameters are defined, in addition to the required number, dimensions & location of reservoirs.
Using smaller flow along longer time makes the "irrigation scheme of operation" (irrigation shifts) a main design tool to reduce the required energy and system pipes & components diameter. The irrigation is then divided to shifts that allow energy & initial expense saving. This detailed design is based on the fact that flow rate in the main line and required flow rate per each irrigation shift is known.
So, if we don't limit the flow in systems with multiple users, the uncontrolled consumption will result with a significant pressure drop in the entire system. This can lead to pump and component cavitation, power consumption overload, air generation, dirt suction, etc. A significant deviation of more than 10-15% from the known design parameters of flow and pressure will result in an irrigation system that functions very poorly. This can be avoided by implementing flow limiting valves.
Higher field demand than the designed flow can take place due to:
- Pipe filling
- Changing irrigation shifts
- Burst
- Filter backwash
- Reservoir filling
Flow Control Applications in Irrigation Systems
1. Pump & system protection
a) Limiting the flow rate at the outlet to the plot in order to protect the pump from over capacity, overload & cavitation conditions and to maintain the design flow rate.
b) Limiting the flow on the main line in order to protect the pump & system from overload and cavitation to maintain a flat pump curve as shown in the graph below. When demand is significantly higher than design:
- The supplied pressure at the field is reduced
- The pump impeller rotates at a very high speed resulting in cavitation conditions and shaft vertical load.
- The power consumption exceeds design parameters, causing higher current usage that might cause pump issues due to the power network overload.
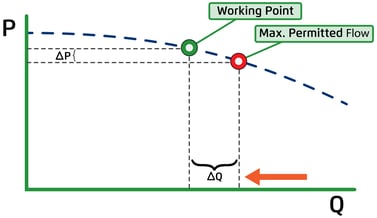
2. Empty lines "fill up" control
Flow control for systems that are emptied between irrigation shifts such as:
- Irrigation machines and center pivots
- Downhill sprinkler systems
- Low pressure non-compensated drip systems
- Pulse irrigation systems
The following video demonstrates an irrigation machine (centre pivot) fill up process:
3. Flow control during filter backwash
Flow control in order to prevent media "run-off" from the filter, screens and potential filter element collapse, in addition to saving water & energy.
The following video demonstrates different control valves required in a filtration system among them, flow control valves:
4. Reservoir fill up & level control
Level control valves regulate when the water level in the reservoir drops. When this happens at the same time that the system is operating/irrigating, it might cause a pressure drop for all other users. So, by limiting the filling flow of the reservoir, we protect the system from this kind of pressure drop. In addition, using a flow & level control valve can provide protection for both valve & reservoir from high filling flow & cavitation conditions.
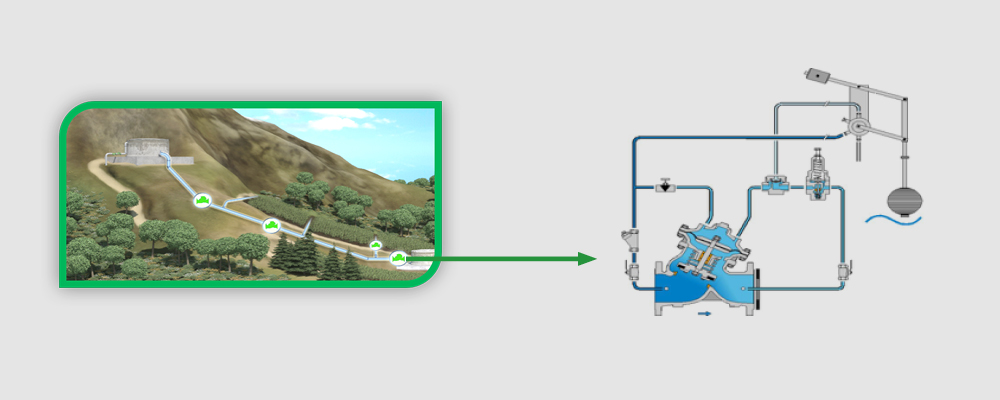
Systems with Flow Control Valves – Principles
- Flow Control Valves react to an increase of the parameters they control by throttling closed.
- This is a "progressive" process = increase in demand results in the valve reducing the flow progressively.
- The more the valve closes, the more the downstream pressure is reduced.
- When demand is lower than design parameters, the valve fully opens.
Should the valve set flow be equal to the designed nominal flow; the valve will constantly be in throttling mode creating higher head-loss (lower downstream pressure at the field) and more demanding operating conditions, risking valve cavitation damage.
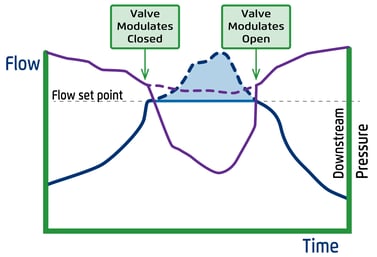
See the graph to the left demonstrating the effect of consumers over demand (light blue area) on valve downstream pressure (purple line) when valve throttles to maintain preset flow (blue line). Note: the dashed purple line demonstrates downstream pressure without flow control; the purple line represents pressure, the blue line represents flow.
Some good reasons to calibrate 10-15% above the design flow:
Bermad strongly recommends calibrating the flow control valve to 10-15% above the plot nominal design flow for the following reasons:
- Should the valve set flow will be equal to the designed nominal flow, the valve will constantly be in throttling mode, the consumers will suffer from low operating pressure and the valve will constantly be under tough operating conditions.
- The chance that all pressurized irrigation system users will irrigate at the same time is statistically low, therefore the risk for excess demand in the system, even when the setting is 15% above the nominal rate is very unlikely.
- Design considerations focus on energy calculations and using valves with minimum head loss is desired. Forcing the valves to constantly be in regulation mode disturbs and contradicts this trend.
- If we set to the nominal flow, the flow rate will not increase even when there is a burst in the plot, preventing the system controller from identifying and alarming in the event of a burst.
Flow Control Valve - Common Flow Sensors & Control Methods
1. Upstream orifice as flow sensorAttached to the valve upstream, the machined orifice plate is sized to create known differential pressure for a given flow rate.
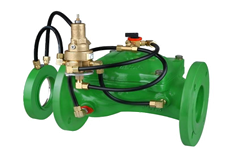
- Should this ΔP rise due to increase in demand, the pilot controls the main valve to throttle close and limit flow to pilot setting. Should ΔP drop due to demand decrease, the pilot controls the valve to fully open.
- The orifice minimum calculated ΔP is 3-4m, to meet pilot sensitivity range, resulting in additional ~2-3m of head-loss on each flow control valve.
- Setting range is ~+20% as it creates increased head-loss across the machined orifice.
The internal differential pressure duct is actually an internal device, installed inside the valve, designed to sense a known differential pressure for a given flow rate. The TubeOrifice’s benefits over the standard orifice are:
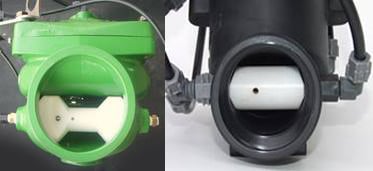
- It's integrated into the valve
- Its added head-loss is a bit smaller; apart from this, the operation principals of flow control valves with "TubeOrifice" flow sensor are identical to those with external ΔP orifice flow sensor.
3. Downstream orifice as flow sensor (for reservoir filling applications)
Located at the valve downstream, orifice differential pressure can be determined by controlling orifice inlet pressure only, as orifice downstream pressure is constant = to reservoir water level. The valve limits the reservoir filling flow by simply reducing the pressure upstream from the orifice (between the orifice & the valve), thereby prioritizing consumers over reservoir filling, and providing level control and valve cavitation protection.
4. Paddle-Type Pilot as flow sensor
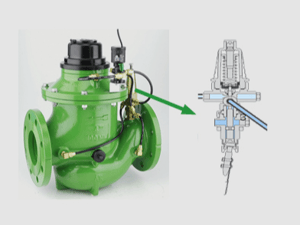
970-55 with Paddle-Type Pilot as flow sensor
Threaded to a dedicated port on the valve body, the paddle type pilot provides 3-Way (or 2/3 Way) flow control capability. Located within the flow stream, the paddle of the pilot is designed to sense the force differential associated with flow velocity "hitting" a paddle. Paddle deviation from the "vertical position", determines pilot control status to throttle close or to open the valve. The image shows a Bermad Flow Control Hydrometer Model 970-55 with Paddle-Type Pilot as flow sensor.
- Should demand rise, flow velocity increases — pushing the paddle so the pilot controls the valve to throttle close and limits flow back to the pilot setting. Should demand drop, flow velocity decreases, allowing the pilot spring to push the paddle back towards the vertical position and the pilot controls the valve to open fully.
- This method is associated with very low head loss (compared to differential pressure sensors) and with a very wide setting range that can be easily adjusted in the field.
Note: For flow velocities below 1m/s, a 2/3-Way Servo Paddle-Type Pilot is recommended.
Flow Control Valves – Project Installations
Outlet Management system Orissa, India
The photos below presents a typical outlet management system in India equipped with flow control & pressure reducing field valves (Bermad Model IR-2"L-172). Each valve controls irrigation of a plot belonging to a different farmer. The project includes 726 Outlet Management Systems (OMS), each including isolation valve, stone trap strainer, air valve, field control valve & automation.
The flow is controlled by 3-Way Paddle-Type Pilots.
Bermad is the chief supplier for this ongoing project with about 3,500 polymeric valves; each was tested & calibrated according to the design requirements at Bermad factory.
Image on the left shows Bermad Model IR-172 Flow Control & Pressure Reducing Valve on test bench for testing & calibration; the right image shows the OMS installation at the site, Orissa India.
Case Study: CCRR Callen in Spain
CCRR Callen in Spain is a 1,872 Ha irrigation consortium with 70 users who grow corn, barley, wheat and alfalfa. The consortium wanted to modernize its irrigation infrastructure because it was outdated, inefficient and required intensive manual operation.
Bermad’s integrated irrigation solution for Callen included a main line & surge solutions as well as remote-controlled pressure reducing and flow-control hydrometers IR-972 to each plot.
The consortium remotely controls each hydrometer according to the designed irrigation shifts.
The flow control hydrometers IR-972 with paddle-type pilot are installed at the irrigation head in order to control:
- Normal irrigation: Securing system pressure and components (pumps, lines, filters, valves, air valves) not to exceed design requirements.
- Pipe filling: Limit line fill-up flow, preventing pressure drop in supply system and possible water hammer associated with high velocity end of line-filling process.
- Burst: Ensuring system functioning even in the event of a pipe burst at the farmer’s end.