Air valves are commonly used in sewage and wastewater systems to increase the system's efficiency by evacuating large volumes of air during pipeline filling and releasing entrapped air and gas pockets during pressurized operation. Air valves provide protection from vacuum conditions by enabling large volume air intake; protecting pipelines during draining or bursts; and providing controlled air relief to reduce potential damage during water hammers or surge pressure.
In this blog, we'll be taking a look at how BERMAD's new C80 Air Valve is designed to tackle some key challenges traditionally experienced in these systems. Here are four reasons why BERMAD's C80 is the go-to solution for effective air control and reduced maintenance costs:
1. Optimized air control — higher efficiency and lower procurement costs
The Challenge
Air valves are engineered products which need to be carefully selected and integrated into the system based on their functionality and air flow capacity. Specifically, they must be selected & specified based upon the compliance of the air flow capacity of the valves with the air control requirements of the system.
Many manufacturers of air valves have published air relief and intake charts which are based on calculations of anticipated air flow. Due to the complexity of aerodynamics inside the air valve during pipeline filling and draining or vacuum conditions, these calculations are biased when compared to the actual air flow capacity. The result is lower efficiency and lower protection from negative pressure (due to lower air flow capacity of the selected air valves) or higher purchasing costs due to the need to use bigger size air valves.
The Solution
BERMAD C80's air relief and intake charts are based on actual measurements carried out by a specialized Air Flow test bench, including negative pressure and vacuum conditions. Measurements are carried out to meet European EN-1074/4 standard and Australian AS4883 standard requirements and are accepted for certification audits.
In addition, the C80 was specially designed to maximize air flow capacity. It has higher than usual air flow compared to other air valves with the same inlet size connections and dimensions.
The C80 data is reliable, allowing the designer to optimize the air control in the system. Its higher air flow capacity offers better value for money and reduces procurement costs.
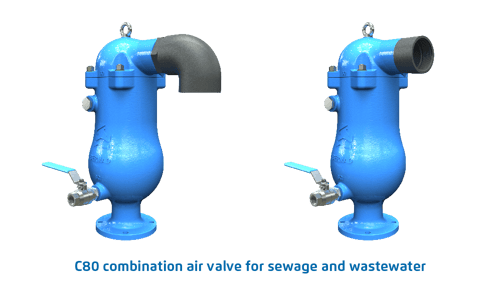
2. Longer operation & easy maintenance — lower maintenance and procurement costs
The Challenge
Accumulated grease and fats as well as suspended & dissolved solids such as napkins and toilet paper or other foreign objects that find their way into the sewage system may clog air valves. To ensure their functionality, air valves need to be maintained (disassembled, flushed and cleaned) approximately every 2-4 months following installation. This means that operators of sewage and wastewater systems have high maintenance costs taking air valves from the field for periodical maintenance and returning them to operation.
Periodical maintenance includes flushing of the air valve's internal mechanism to remove dirt, grease and foreign particles that can interfere with air valve operation.
The Solution
C80 air valve are specially designed for longer periods of operation and easy maintenance.
All the internal parts of the valve are manufactured from Type 316 stainless steel and polypropylene and are fully corrosion resistant. They are also built for high endurance — the lower float can endure 55 bar, 800 psi.
BERMAD's experience has shown that using the additional surge protection feature reduces the velocity of the approaching water into the air valve chamber and also contributes to preventing grease and solids from reaching the upper mechanism of the air valve. The result is longer periods of operation without the need for maintenance.
For periodical maintenance, BERMAD C80 can be opened from the top and the internal assembly can be easily removed for quick replacement. Access to flush and clean the automatic and kinetic orifices is quick and easy. The ability to open the C80 from the top is also critical for installation in small pits.
In addition, the BERMAD C80 has two service ports and drainage valve which enable draining and back flushing in the workshop or in the field.
All the above features enable longer periods of operation without maintenance and reduce operation costs.
Click to watch C80 quick maintenance video
3. Low pressure conditions — preventing leakage
The Challenge
A known weakness of air valves is that they tend to leak at low pressure. Relatively low pressure occurs after pump shutoff or at high points at the end of the pipeline. In these cases, the force which pressurizes the seals (comprised of the system's pressure and buoyancy of the float) will not be enough to seal the orifices.
Unlike air valves for clean water, where some leakage during pipeline filling or automatic air release might be tolerated, in the case of sewage and wastewater systems, there is zero tolerance for leakages.
Not only does leakage from sewage and wastewater air valves cause damage to the environment, the maintenance team has to take care of it, which causes higher maintenance costs. In some cases, the maintenance team is forced to isolate the air valve in order to prevent the leakage — which means that the air valves installed to increase efficiency and protect the system from vacuum conditions have been neutralized.
The Solution C80 was specially designed to cope with low pressure conditions of low pressure sealing of 0.8psi, 0.05 bar which prevents leaks and reduces maintenance costs. |
![]() |
Click to watch C80 principle of operation video
4. Pump start up — preventing damage to air valves and water hammer in the system
The Challenge
Aggressive pump start-ups to pump fluids with suspended solids into the pipeline creates risks for surge pressures. When the water enters the air valve chamber at relatively high velocity, there's always a risk that the float assembly will be slammed towards the upper part of the valve, creating damage to the air valve and water hammer in the system.
The Solution
BERMAD's surge protection device is threaded to the C80 air valve outlet, so that when the velocity and pressure increase, the outlet is partially closed and the approaching water is slowed down, while air relief continues.
While this feature is optional, we strongly recommend the surge protection device for every air valve, preferably installed near the pump or at high points, as it not only prevents damage to the system but also reduces operation and maintenance costs.
The Bottom Line
BERMAD's C80 offers optimal performance which ensures efficient pipe line filling, lower energy consumption during pressurized operation, protection from vacuum conditions, as well as reduced maintenance costs.