Industrial fire protection valves are designed to be robust, but even the toughest valve body can crack or break when subjected to the pressure exerted upon it from inside by the expansion of water as it freezes. In environments where freezing temperatures are likely or even possible, it is important to protect your deluge valves from this possibility. A number of solutions exist to protect deluge valves from freezing. Let’s explore the pros and cons of each.
Below Ground Deluge Valve Installation
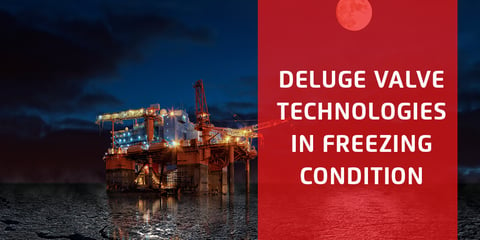
Soil is an excellent insulator, and one reliable way to keep deluge valves from freezing is to install them underground below the frost line. Even if the outside temperature is very low, the water inside the pipes and valve in an underground installation will remain in a liquid phase. Despite the necessity of building a chamber or small underground room to house the valves, below ground installation can be quite cost effective because it is usually not necessary to supply supplemental heat to the area.
The biggest drawback to installing deluge valves underground is accessibility. There is no direct line of sight between the valve and the area it protects. In order to activate or service the valve, someone must be physically present to open the chamber cover. Typically, the valve can only be accessed by means of a ladder. In a fire situation where every second counts, even a 30 second delay to open the cover and climb down to the valve can represent a significant safety compromise.
Another issue that can prove to be problematic with underground deluge valves is drainage. Pumps are typically required, and should the drain or pump fail, excess water has nowhere to go other than to fill the chamber, where it can damage sensitive equipment.
Heat Tracing
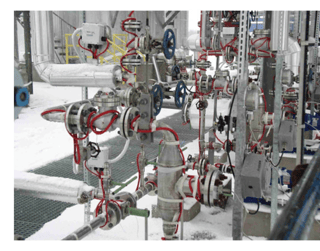
Another common way to protect pipes and valves is to use a heated cable to keep the components warm. This can be a cost effective method of freeze protection in the short term because there is no need to build any special infrastructure: just string the cable and cover with insulation. However, this solution is often not ideal in the long term.
The biggest problem associated with heat tracing is the necessity of moving or removing it when the valves are serviced. It is often next to impossible to return the cable to its original position after routine valve maintenance; the shifting that commonly occurs after re-installation can leave valves vulnerable to freezing.
Heat tracing is best used with pipes that only need to be removed if a pipe is leaking. For deluge valves that must be serviced, other options are recommended.
Heated Cabinet
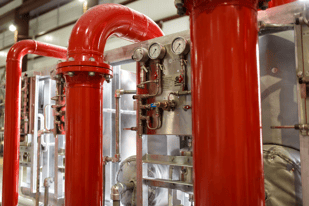
An excellent solution for deluge valve freeze prevention is to construct a heated cabinet to house the valves. This provides similar benefits to an underground installation while avoiding most of the accessibility issues.
A programmable thermostat mounted inside the cabinet ensures that the heater turns on during freezing conditions to keep valves and pipes above freezing temperatures. Heated and insulated cabinets can be constructed to house the control trim only, or for the full system.
Combination of Methods
Determining the optimal deluge valve freeze prevention method to use depends on many factors, including budget, climate, site constraints, and system design. Often, no single solution is ideal. In such cases, the best approach is often to combine freeze prevention methods to create a custom solution for the site.
For example, if building a full size heated cabinet is cost or space prohibitive for a particular application, you can consider an approach such as enclosing only the deluge valves in smaller cabinets, in conjunction with heat tracing and permanent insulation on pipes. Or, perhaps you might choose to have a deluge valve installed below ground, with pneumatic activation installed in a small cabinet above ground level.
Custom Freeze Prevention Solutions, From Design to Delivery
At BERMAD, we understand our customers’ needs for flexibility and innovation. We are available to provide custom solutions as needed. These can range from something as simple as assembling the pressure gauges visible to the operator from ground level, to an entire turn-key project designed, manufactured and delivered to the site.
To learn more about how we can help you determine the ideal deluge valve freeze prevention solution for your application, contact us to speak with a BERMAD representative in your region.