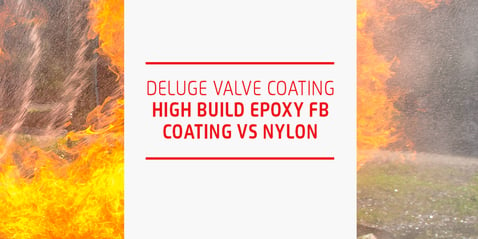
Even more than most industrial fittings, fire protection valves require the utmost in reliability throughout their service life. Every part of the valve must be designed with this in mind, including the valve body itself.
Most fire protection valves are made from Ductile Iron or Cast Steel material. These metals provide excellent strength and durability, but they are susceptible to corrosion Therefore it is imperative to protect the entire exposed surface of the valve body from its environment. This is especially true for valves intended for use in harsh or corrosive conditions, such as seawater, corrosive off-shore atmospheres or intense UV exposure.
This is why valve coatings are so important. Coatings improve valve performance in three ways:
- They provide that critical protection, Isolating the valve from its environment, thus extending the serviceable life of the valve.
- Valve coatings also help prevent the occurrence of mineral buildup and obstruction in important water pathways or narrow spots in the valve.
- And, they contribute to a more efficient pathway by helping to reduce the friction coefficient of the valve.
The type of coating used on a valve is therefore an important thing to consider when selecting fire protection valves. Many valves on the market today feature thermoplastic powder coatings. While thermoplastic valve coatings can be appropriate for certain specific situations, we normally recommend and manufacture valves that feature our high build fusion epoxy valve coating system. Here’s why:
4 Advantages of BERMAD High Build Fusion bonded Epoxy over Thermoplastic Fire Protection Valve Coatings
- Superior Adhesion: It’s difficult to distinguish one type of newly-applied valve coating and another just by looking at it. But over time, the difference becomes apparent. The valve whose coating adheres best to the valve body material will always outlast the competition. In our experience both in the lab and in the field, our fusion bonding epoxy (FBE) has 2-4 times better adhesion than thermoplastic coatings - a parameter that is considered to be the most important in protective coating systems.
- Continuous Coating Seal: In a corrosive environment, even the smallest pinhole in a coating will allow corrosive environmental agents to reach the valve body. When this happens, the valve will quickly begin to corrode, and its useful life will be shortened considerably. Therefore when a valve coat is applied, the layer must be pinhole-free both inside and out to ensure a perfect coating.
When coating a component like a deluge valve that has a complex shape, it can be challenging to maintain a consistent thickness in the coating, which is important for preventing pinholes and voids. The larger the particle size, the more difficult it is to achieve a consistent, pinhole-free coating, because the minimal thickness required for a layer needs to be 2-3 times higher than particle size. Particle size in an FBE coating is about two times smaller than that of thermoplastic coatings. So for instance an FBE coating with a particle size of 40 μm can be made pinhole-free with a 100 μm layer. In contrast, a thermoplastic coating with a particle size of 100 μm will require a 200 μm layer. An FBE coating thus offers far more reliability in ensuring a continuous coating film.
Seawater valves especially are subjected to a holiday detection test to ensure a continuous coating film free of even the smallest pinhole or void that could compromise valve integrity. - UV Resistance: BERMAD valves can be found installed in the harshest conceivable environments, from the southernmost reaches of Argentina to northern Russia. In addition to extreme temperatures and corrosive chemical environments, many of these valves have to hold up to intense direct sunlight, which in the polar regions can occur for nearly uninterrupted stretches for months at a time.
While thermoplastic has superior UV resistance over unmodified epoxy, BERMAD has developed a polyester top coating which provides even greater UV resistance. Rather than reducing adhesion, the UV resistant top coat fuses together chemically with the high build epoxy in such a way that the two coating layers function as a single layer, thus providing the best possible coating solution for high UV environments. - High Temperature Resistance: In a fire protection valve it is crucially important for the control trim to remain perfectly positioned so that it continues to function despite being exposed to high temperatures. The term “thermoplastic” refers to this type of coating’s ability to melt at high temperatures. However, having a melting point is not always an advantage. Should a fire occur, fire protection valves can be exposed to extremely high temperatures—high enough to possibly re-melt a thermoplastic coating and cause it to drip. As a thermoplastic coating melts, it might drip into the inner workings of the valve or the system and damage it. Because high build epoxy doesn’t melt, it precludes the possibility of a coating to interfere with the proper functioning of the valve at a critical moment.
BERMAD does offer the option to manufacture thermoplastic valve coatings for special applications upon request. However, such situations are rare. For the vast majority of applications, the high build epoxy system offers superior protection and fail-safe performance.
To learn more about BERMAD fire protection valves, or for assistance in valve selection, click here to contact a BERMAD fire protection representative in your region.