A critical thing to know about any piece of equipment is its mean time between failures (MTBF). MTBF is the measure of time it takes between installing the equipment and when it can reasonably be expected to fail. In other words, it is a measure of reliability.
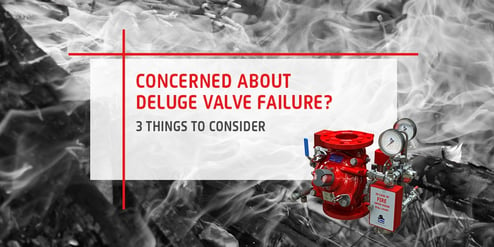
In the case of fire protection equipment, deluge valves present a unique challenge to the MTBF testing process. That is because they are designed to sit inactive for long periods of time. Typically, fire protection deluge valves are mechanically tested every three months and given an annual test run. Aside from that they are designed to simply hold back the flow of water from protected areas for years, unless or until the day comes when they are needed and asked to function. They therefore are subject to very little of the normal wear and tear that affects more heavily used types of valves.
To put it in perspective, let us say, the average life span of a valve is 5,000 hours of use. Meaning that it would take over 100 years to get that kind of usage out of a deluge valve.
So the actual chance of a well-maintained high-quality valve failing under typical conditions is extremely rare. However, MTBF does not embody the entire aspects that contribute to the reliability and life span of the valve.
Perhaps a better way to approach the question of life span in a deluge valve is to think about what situations might lead to failure, and proactively avoid them.
1. Choosing the Right Deluge Valve for the Application
The first thing to consider is that a deluge valve is an engineered product, designed to meet particular criteria depending on the site and application at hand. Therefore the first line of action is to select the correct valve model and materials of construction for the project. This includes considering the type of fluid the valve will be expected to service; environmental conditions such as salt water, freezing temperatures and corrosive environments; and the basic flow and pressure characteristics of the system. For example, if it is known that a valve will be installed in a corrosive environment, specifying appropriate construction materials will help prevent premature failure of the valve due to corrosion.
2. Preventing Deluge Valve Failure Due to Fire Water
The #1 external influence that can cause failure in a correctly selected valve is the supply water. Our deluge valves feature one of the straightest flow patterns on the market, but there is some interesting debris to be found in fire water. You can have the most reliable car in the world, but when you put funky gas in it you are inviting problems; in the same way, even the best designed valve risks failure if it is asked to handle water that is chock full of debris. Because BERMAD deluge valves have no mechanical moving parts and are therefore highly reliable, 99% of the issues we see with valve performance can be traced to debris in the water—this despite the fact that our diaphragm is supported and fairly well protected in both closed and open positions, and the incidence of problems is extremely rare.
Unfortunately, strainers are often not considered, but they are an inexpensive solution that prevents sprinkler heads from clogging as well as keeping valves clear of debris that might cause them to fail prematurely. Installing basket or Y type strainers before the valves in a deluge system represents only 0.5 to 1 percent of the total budget for a typical project and effectively eliminates the potential for valve failure due to fire water debris.
3. Damage to or Improper Assembly of Unit
The last type of deluge valve failure that can occur is when the valve has been damaged during routine maintenance or not properly set up. Here again, strainers can sometimes save the day; damage can sometimes occur when someone has had to clear out debris from a valve because there was no strainer in place, or if there was trash in the flow path when a valve was closing. It is also possible to make mistakes when replacing elastomers or solenoids.
This is one reason we don’t leave the trimming of our valves for the end user or contractor. Unlike some deluge valves, which are delivered separately from their components, each BERMAD valve comes pre-trimmed from the factory, and is tested - Hydrotest , Leakage & Functionality - before it leaves the facility. That way, there is no chance for improper assembly to compromise performance.
A Proactive Attitude Leads to Optimal Reliability
Most people think of a fire protection system as a burden…until they need it. While deluge valves are inherently very reliable, it makes sense to do everything possible to ensure maximum possible reliability for your deluge system. Bermad adapted the highest standard testing method and QA supervision to reduce the probability for such failures to happen.
For more information about creating the most highly reliable fire protection system for your application, or to speak with a BERMAD representative in your region, contact our fire protection division here.